Metal Polishing vs. Grinding: Key Differences & Applications
- Kevin Lim
- Apr 11
- 4 min read
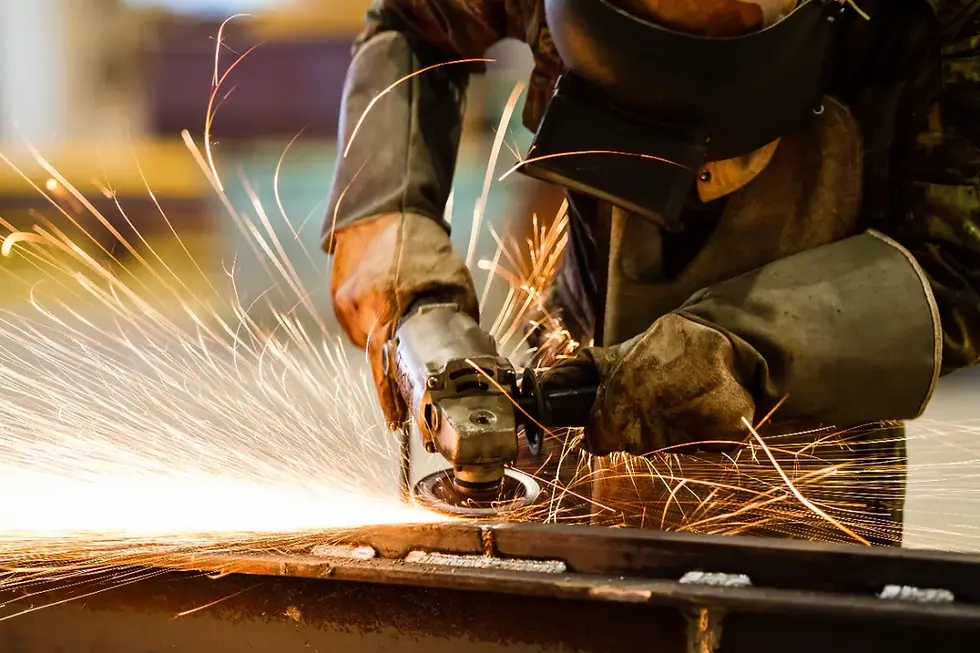
In metalworking, achieving the right surface quality is essential for both functional and aesthetic reasons. Two common methods used to refine metal surfaces are grinding and polishing. While both techniques enhance the finish of metal components, they serve distinct purposes and are applied in different ways. For manufacturers, particularly those in a machine shop setting, understanding these key differences can help in selecting the most suitable process for precision components.
This article explores the fundamental differences between metal grinding and polishing, providing valuable insights into when and why each method should be used, especially in industries such as manufacturing and metal finishing in Singapore.
Defining Metal Polishing and Grinding
What is Metal Grinding?
Grinding is a machining process that involves the use of abrasive tools to remove material from a metal surface. It is primarily used for shaping, sizing, and refining components to meet specific dimensions and tolerances. This process is highly effective for removing excess material, correcting surface irregularities, and preparing the workpiece for further finishing.
Common tools used in grinding include grinding machines equipped with abrasive wheels, belts, or discs. The choice of abrasive depends on the hardness and type of metal being processed. Grinding is widely used in manufacturing industries where precision and accuracy are crucial, such as automotive, aerospace, and heavy machinery production.
What is Metal Polishing?
Polishing, on the other hand, is a finishing process designed to create a smooth, reflective surface by eliminating minor imperfections. Unlike grinding, which focuses on material removal, polishing enhances the surface’s appearance and texture without significantly altering its shape.
The polishing process involves the use of polishing pads, cloths, or soft abrasives combined with fine polishing compounds. It is commonly applied in industries where aesthetics and surface smoothness are critical, such as medical instruments, punch and die for drawing applications, and coining applications.
Process Overview
The Grinding Process
Grinding begins with a coarse abrasive to quickly remove material and shape the workpiece. As the process continues, finer abrasives are used to refine the surface and improve dimensional accuracy. The key parameters in grinding include:
Speed and Pressure: Excessive force or high speed can generate heat, leading to surface damage or deformation.
Coolant Application: Using coolant helps to prevent overheating and extends the lifespan of the grinding tool.
Abrasive Selection: Different metals require different abrasives to achieve optimal results.
Grinding is often used as a preparatory step before polishing, ensuring that the surface is smooth enough for the final finishing process.
The Polishing Process
Polishing follows grinding in many cases, using progressively finer abrasives to achieve a mirror-like finish. The process typically involves multiple stages:
Rough Polishing: Removes minor scratches and imperfections left after grinding.
Intermediate Polishing: Uses finer abrasives to improve the finish.
Final Polishing: Achieves the desired smoothness and reflectivity using ultra-fine compounds.
Polishing requires careful handling, as excessive pressure or incorrect technique can introduce new surface defects.
Key Differences Between Grinding and Polishing
Purpose and Outcome
Grinding is used to remove material, refine shapes, and correct imperfections.
Polishing is aimed at enhancing the surface finish, reducing roughness, and improving visual appeal.
Material Removal Rate
Grinding has a high material removal rate, making it suitable for rapid shaping and sizing.
Polishing removes minimal material, focusing on surface refinement rather than structural changes.
Surface Finish
Grinding results in a matte or slightly rough surface, depending on the abrasive used.
Polishing produces a smooth, reflective, and often mirror-like finish.
Applications of Grinding and Polishing
Where is Grinding Used?
Grinding is essential in industries requiring precise shaping and sizing of components. Common applications include:
Preparing metal surfaces for welding.
Manufacturing tools and machine parts with tight tolerances.
Removing rust, oxidation, and unwanted coatings from metal surfaces.
Where is Polishing Used?
Polishing is ideal for applications where surface smoothness and appearance are key. Common uses include:
Punches and die components for half-cut, coining, and drawing applications.
Finishing medical instruments to ensure hygienic surfaces.
Reducing friction in components such as gears and bearings in plastic moulding applications.
Benefits and Limitations
Advantages of Grinding
Efficient material removal, allowing for rapid shaping and preparation.
High precision in achieving specific dimensions and tolerances.
Suitable for hard metals and heavy-duty applications.
Limitations of Grinding
Can cause surface damage if not properly controlled.
May leave visible grinding marks and directional patterns, requiring additional finishing.
Generates heat, which can affect metal properties if not managed with coolants.
Advantages of Polishing
Creates a smooth, reflective surface, improving aesthetics.
Enhances corrosion resistance by reducing surface roughness.
Improves functionality in moving parts by reducing friction.
Limitations of Polishing
Time-consuming and labour-intensive compared to grinding.
Higher costs due to the use of fine abrasives and skilled labour.
Not suitable for shaping or removing large amounts of material.
Selecting the Right Process for Precision Components
When deciding between grinding and polishing, manufacturers should consider several factors:
Material Type: Some metals are easier to grind, while others respond better to polishing.
Intended Function: Components requiring low friction or a decorative finish benefit from polishing, while structural parts may need grinding.
Production Costs: Grinding is generally more cost-effective for shaping, while polishing requires more time and skill.
In many cases, a combination of both methods is used to achieve optimal results.
NVT Technology’s Expertise in Metal Finishing
Understanding the differences between grinding and polishing is essential for selecting the right finishing process for precision components. While grinding ensures accurate shaping and sizing, polishing enhances surface quality and performance. At NVT Technology, a trusted name in metal and carbide polishing in Singapore, we specialise in advanced metal finishing solutions tailored to diverse industry needs.
With expertise in both grinding and polishing, we provide high-quality services that enhance the durability, functionality, and appearance of metal components. Whether you operate a machine shop or require precision finishing for industrial applications, our commitment to precision and excellence ensures that manufacturers receive the best possible results.
For expert guidance and professional metal finishing solutions, trust NVT Technology to meet your needs with precision and efficiency.
Comments